Using liquids for plastic colouration – the best solution?
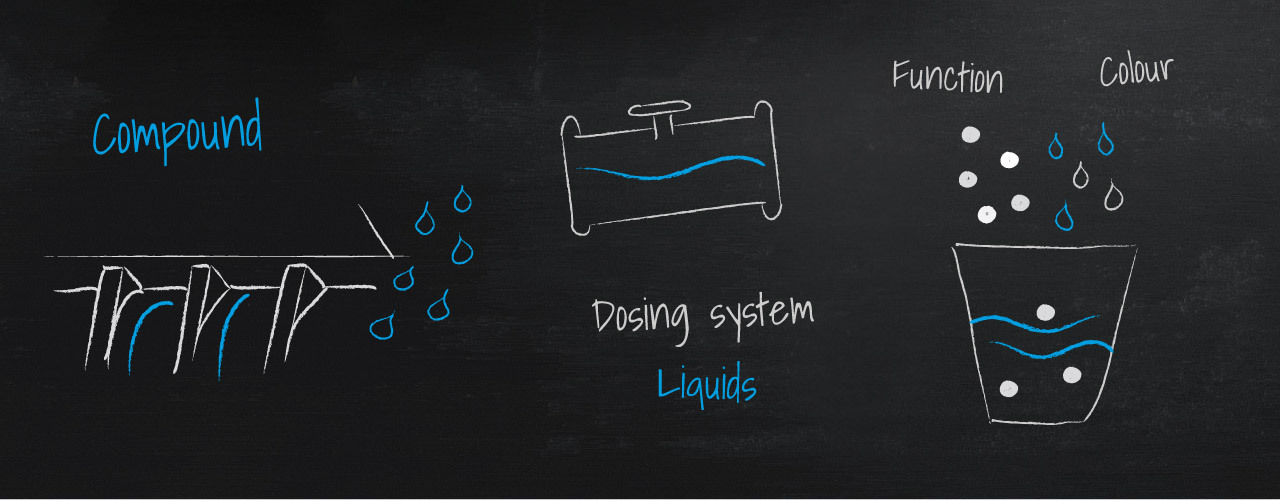
The colouration of plastics is generally achieved through the use of colour masterbatches (concentrated mixtures of pigments) in a carrier material. These preparations are time-consuming and costly to make, since they must be adjusted specifically to suit the type of plastic and/or the kind of part being produced. The wrong choice of carrier material can result in immiscibility and thus in major problems during the colouration process. Unsuitable formulations may lead to the formation of deposits on tools. In other cases, segregation during the melt process can lead to marks on the part or even to traces of colour in the feed systems.
In light of the above, we have to consider whether the effort of producing a concentrated mixture and carrying out the associated production process is actually worthwhile. Attempts to select a cheap “universal polymer carrier” – and putting up with the associated labour- and cost-intensive cleaning process and increased scrap rates – have been of doubtful merit. While there are a number of advantages to using granules as a raw material in plastics processing, particular applications necessitate the use of other methods of colouration. Particularly in the case of translucent colours and plastics with colour and functional requirements, liquid dosing provides a real alternative to existing solutions.
How does the preparation work?
The liquid colouration process involves a system comprised of a binding agent, various colorants and other additives, including processing additives, stabilisers and other similar substances. Typical binding agents include fatty acid esters or fatty acid ester ethoxylates, paraffin oils, polyhydric alcohols or alcohol ethoxylates. Mixtures containing the latter two substances can also serve as binding agents. The choice of binding agent is determined by the type of plastic. The pigment preparation is very easy to produce. The components of the mixture are dispersed in a binding agent (selected in advance for its suitability for the application) and then distributed. The break-up of agglomerates should occur at an optimal rate to guarantee the effectiveness of the colour concentration and/or functional process additives.
Does liquid colouration have any major disadvantages?
A significant disadvantage of liquid colouration is the low opacity of the resulting colours and – to some extent – the temperature behaviour of the binding agent, which must always be selected on the basis of the thermoplastic to be treated and for which a number of near-universal options are available, particularly in the area of high performance plastics. The danger of segregation in modern binding agents is virtually non-existent, while peristaltic pumps and a fast-closing system keep cleaning requirements to a minimum. In addition, traces of residual colour on machine components, on the floor or on clothing and hands can easily be wiped away or washed out.
What are the advantages?
Provided that you have the necessary peripheral equipment, liquid colouration of plastics offers a number of significant advantages. The excellent wettability of individual granules and the resultant good distribution of colour achieve highly uniform coverage. The thorough dispersion of colour pigments ensures that full colour strength is obtained and thus that a very high cost-benefit ratio is achieved. Particularly when it comes to processing additives and stabilisers, there are also many chemical compounds that are available only in liquid form and must be prepared as powders via a number of labour-intensive processes before being used in conventional colouration processes. The fact that liquid colorants can be combined cheaply with possible additives makes this kind of compound preparation highly effective and (to some extent) universally applicable.
How does liquid colouration compare in terms of cost?
Some areas of application within the plastics industry require high flexibility. In these situations, colouration of plastics using masterbatch techniques may be a better option than liquid colouration. However, when we consider that masterbatch must be fed into the process via an additional feed system, leading to a higher rate of error, we see why the above statement is not always the case. When it comes to plastic compounds, liquid colouration is cheaper, ensures optimal utilisation of materials and draws all its material from a single source. For these reasons, producing quality-tested, dyed plastic compounds is often more cost-effective than adding masterbatch. The former method also has the advantage of eliminating the difficulties mentioned in the introduction in relation to part production and materials handling.
Interested in purchasing coloured plastics from POLYMERWERKSTATT?
We offer fully customised thermoplastics within made-to-measure product solutions. Whether your requirements relate to form, colour or both, our products fulfil the highest standards of quality and are suitable for use with food. Contact us for more information!